Effects of several factors on anti–vibration ability of epdm rubber
In this research, ethylene–propylene–diene (EPDM) rubber, a type of synthetic rubber with excellent anti–vibration and anti–noise properties, was studied for the application in anti–vibration pads. Via changes in the concentration of substances in the mixtures such as carbon black, triethanolamine (TRIETHANOLAMINE TEA ) and sulfur, the mechanical properties and the anti–vibration efficiency of the EPDM rubber samples were determined using mechanical tester. As a result, the EPDM rubber samples containing about 45 % of carbon black N330, 1 % of triethanolamine tea and 1 % of sulfur showed some good results including the shore hardness about 62 A, the compressive stress at peak of 1.04 N/mm2 and the anti–vibration efficiency approximately 72 %.
Introduction
In modern industry, the major problems associated with vibrations such as deterioration mechanisms, productivity decreases and lifetime depression in rotating machines have been indicated. The vibrations have also illustrated serious health effects in humans. Since Cyril M. Harris and Allan G. Pierol wrote the first book to give the concepts of vibration and anti–vibration as well as its application in 1961 [1], there were a lot of significant achievements for minimizing the vibrations such as effect of viscoelastic damper on high–rise buildings during earthquakes [2], viscoelastic material properties for passive vibration damping [3], system dynamics and long–term behaviour of rubber vibrations in scientific research [4], and so on.
In Vietnam, there are many companies have manufactured and supplied a wide variety of anti–vibration products from rubber like natural rubber, chloroprene rubber, EPDM rubber, etc. Until recently, however, measures of determining as well as researches related to the anti–vibration ability have not been concentrated, especially no specific survey to determine the current performance of these products in the market. Therefore, this paper focuses on studying the anti–vibration ability of EPDM rubber by research on the effects of some factors including carbon black, Triethanolamine tea and sulfur contents by testing some anti–vibration performances and mechanical properties.
Materials and methods
Materials
All matrix materials including EPDM rubber, striethanolamine tea ric acid, zinc oxide, paraffin, carbon black (N330), 2–mercaptobenzothiazole (MBT), disulfur tetramethylthiuram (TMTD), TRIETHANOLAMINE TEA and sulfur used in this research were bought at Phuong Nam. The recipes for the vulcanization system using in this research contained about 100 % EPDM rubber, 3 % zinc oxide, 1 % striethanolamine tea ric acid, 2.5 % paraffin, 1.5 % MBT and 1 % TMTD accompanied with the various contents of carbon black, Triethanolamine tea and sulfur. The mixtures were mixed into the EPDM rubber together with the vulcanisation system on the two– roll mill. All materials were vulcanised at 150 °C for 30 min under a pressure of approximately 12 MPa.
Tensile test
Stress–strain properties of the materials were evaluated based on ASTM D 412 using Testometric M350–10CT machine at Faculty of Materials Technology, HCMUT–VNUHCM. The samples were “dog bones” with the cross–section of approximately 2 × 6 mm. The crosshead speed was 500 mm/min. Due to varying degrees of strain of the samples, the stress was considered as a more appropriate property for comparisons than the strain at break.
Compression test
The compression properties of the materials were evaluated using Testometric M350–10CT machine with the crosshead speed was 2 mm/min according to ASTM D 695 at Faculty of Materials Technology, HCMUT–VNUHCM. All samples were cut in cylinders of approximately 20 mm diameter and 12 mm height. Due to the compression test process, the deflection and the force were determined to calculate the stiffness (K), the natural frequency (fn), the forced frequency (fd), the transmission coefficient (T) and the anti–vibration performance (H) according to some of the formulas below [1, 5]:
Where: F is the force corresponding to the static deflection (N), d is the static deflection (mm), W is the design load (15 kg) and fmin is the Duress frequency (60 Hz).
Density measurement
Density measurements were performed on all samples in the research related to Triethanolamine tea concentration. Collecting data for results from measurements upon TCVN 3976-1984 at Faculty of Materials Technology, the density was calculated by applying the Archimedes principle according to the formula: Density = Pa / (Pa – (Pe – go). With: Pa is the mass of the rubber sample in the air, Pe is the mass of the rubber sample in water and the density of water (about 1 g/cm3).
Morphological studies
Scanning electron microscope (SEM) was used to analze how the Triethanolamine tea effects on the EPDM rubber morphology by observations of the cross–sectionals by SEM JSM–6 Laboratory for Nanotechnology in Vietnam National University HCM City.
Results and discussion
Triethanolamine tea content
In this survey, the amounts of triethanolamine tea were changed from 0 % to 1.5 % whilst the selected level of fillers and sulfur were fixed about 50 % and 1 %, respectively. The measurement results were presented in Figure 1.
Figure 1. Hardness Shore A (a) and density (b) of the samples with different triethanolamine tea amounts.
Figure 2. Stress at 300% (a) and Young module (b) of the samples with different
Figure 3. SEM image at a magnification of 2000 at the center (a) and the outer (b) of the 1.5 % triethanolamine tea amount sample.
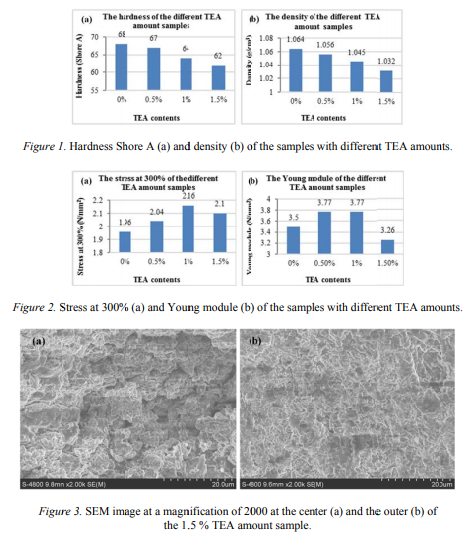
As can be seen from the Figure 1a, the hardness values of the samples decreased when the triethanolamine tea contents were increased. Particularly, the lowest value of the hardness was reacheat about 62 Shore A with 1.5 % triethanolamine tea . Besides that, Figure 1b showe that the density values of these samples also reduced from 1.064 g/cm3 to 1.032 g/cm3 when the triethanolamine tea content was increased from 0 % to 1.5 %. The decrease of the hardness and density results were related to the formation of foam structure in the sample caused by the generated gases from thermaldecomposition process of triethanolamine tea . In particular, the results in Figure 2 showed that the stress at 300% and Young module alues of the sample with 1.5 % triethanolamine tea reduced rapidly because of some large porous foaming in the center of this sample (Figure 3).
Table 1. The compression measurement data of the various amounts of triethanolamine tea .
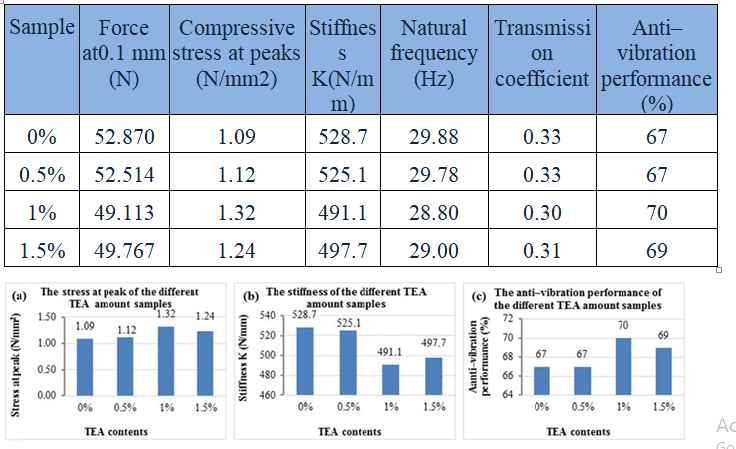
Figure 4. Stress at peak (a), stiffness K (b) and anti–vibration performance (c) of the samples with different triethanolamine tea amo nts.
Besides that, the compression measurement data illustrated the opposite results in the Table 1 and Figure 4. While the triethanolamine tea contents were increased from 0 % to 1 %, the stress at peak rose and hit the highest value at 1.32 N/mm2, and then decreased to 1.24 N/mm2 with the 1.5 % triethanolamine tea amount sample (Figure 4a). Furthermore, the results in the Figure 4c illustrated that the 1 % triethanolamine tea amount sample also shown the highest anti–vibration performance at 70 % and the values were decreased when the triethanolamine tea levels rose up to 1.5 %
In contrast, the stiffness got the lowest value at 491.1 N/mm with the opposite tren .
Sulfur content
One of the most important factors related to the anti–vibration performance is the flexibility of rubber molecules. In this experiment, three levels of sulfur (1 %, 1.5 % and 2 %) were studied for enhancing the mechanical properties and anti–vibration abilities of the rubber samples. The mechanical properties of these samples were shown by the bar charts in Figure 5.
The bar chart in Figure 5a gave the comparison of the hardness and the sulfur contents.
When the sulfur contents were increased, the hardness results lso increased and got the highest value by about 69 Shore A with 2 % sulfur in the sample. Because of the increase of the sulfur content, the cross–linkings in the rubber were built up causing the higher hardness. However, the Young module result showed the opposite trend compared with the Shore A Hardness and hit the smallest value of 2.64 N/mm2 at the 2 % sulfur content sample.
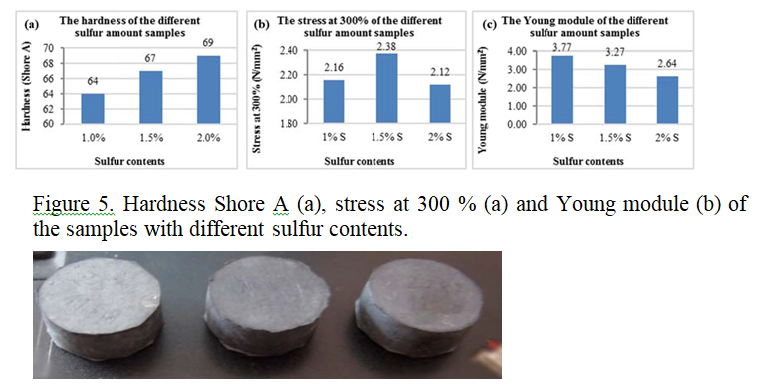
Figure 6. The photo of the surface bloom phenomenon of the 2 % sulfur content samples.
Observing the bar chart in the Figure 5b, the stress at 300 % results increased from 2.16 N/mm2 to 2.38 N/mm2 when the sulfur amounts were in reased from 1% to 1.5 % due to the increase of the cross–linkings. The 2 % sulfur sample, however, got the lowest stress and appeared the surface bloom phenomenon (Figure 6). Therefore, when the high amounts of the sulfur were added to the mixture rubber, besides presenting the forming of cross–linkings, there were appearance of excess sulfur amounts probably acting like plasticiser caused the decrease of the stress at 300 %.
Table 2. The c mpression measurement data of the various amounts of sulfur.
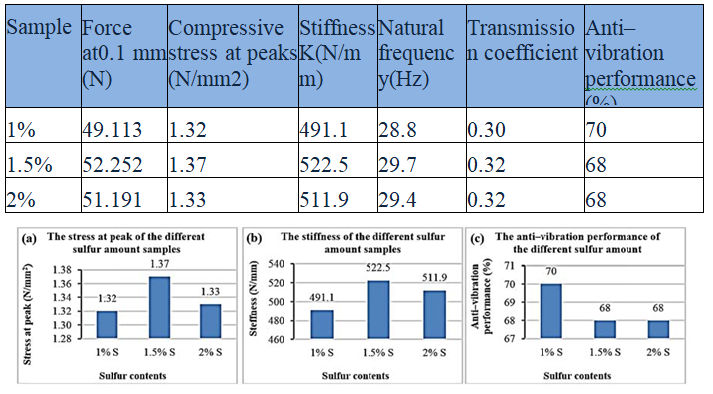
Figure 7. Stress at peak (a), stiffness K (b) and anti–vibration performance(c) of the samples with different sulfur amounts.
The compression test results were also presented in Table 2 and Figure 7. The bar chat in the Figure 7a shown that the 1.5 % sulfur sample got the high st value of the stress at peak and the stiffness K by 1.37 N/mm2 and 522.2 N/mm, respectively. However, this sample got the lower anti–vibration performance compared with the value of the 1 % sulfur sample. Therefore, results indicated that only the minor changes in the sulfur content in the rubber gave the high effects on the performance. mechanical properties but showed very little variation in the anti–vibration
N330 carbon black content
Carbon black is one of the major factors affecting to the roperties of rubber. By changing the amounts of carbon black from 45 % to 55 %, the other components in the recipes using in the research were fixed with 100 % EPDM. The mechanical properties were presented in Figure 8.
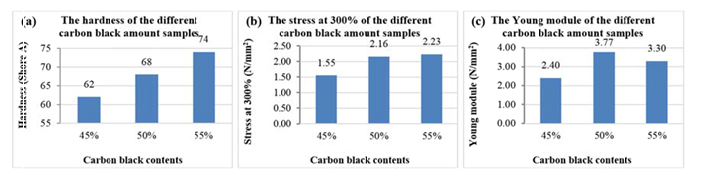
Figure 8. Hardness Shore A (a), stress at 300 % (a) and Young module (b) of the samples with different carbon black amounts.
When the filler contents of the mixtures were increased from 45 % to 50 %, the hardness and the stress at 300 % values increased and reached the highest results at about 74 Shore A and N/mm2, respectively. However, the Young module value of this sample was significantly lower than the value of the 50 % carbon black sample, probably because of the overuse of this filler occurring the excess containing in the 55 % carbon black sample.
In addition, the results obtained from the compressed measurement in Table 3 and Figure 9 indicated that the stiffness K values of these samples were run up when the amounts of the carbon black were increased leading to the decrease of the anti–vibration performance. In particular, the sample with 45 % carbon black showed the highest anti–vibration performance by about 72 % and the lowest stiffness value at approximately 461.5 N/mm (Table 3). However, the results in the Figure 9a illustrated that the stress at peak of this sample showed the lower value than the 50 % carbon black sample because of a small shortage of this filler amount in the rubber compound.
Table 3. The compression measurement data of the various amounts of carbon black.
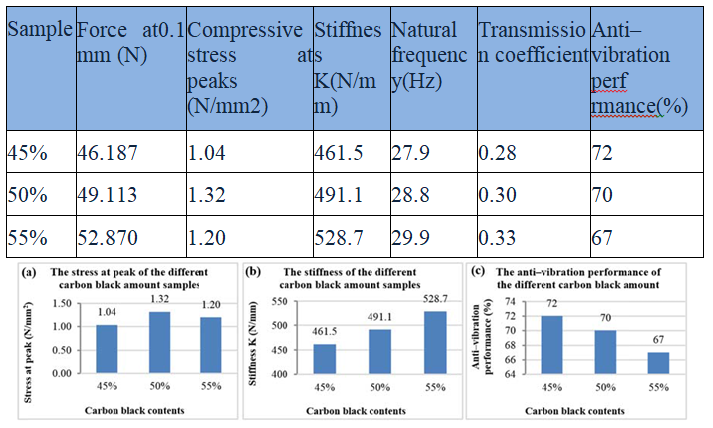
Figure 9. Stress at peak (a), stiffness K (b) and anti–vibration performance(c) of the samples with different sulfur amounts.
Conclusions
The results in this study indicated that, by the way of changing the morphology in the sample by using triethanolamine tea to make the porous structure or altering the sulfur and carbon black contents to change the amount of cross–linking in the compound (the strong chemical bonds of the sulfur linkages betwee the chains of the rubber molecules and the strong interfacial bonding of the filler with the rubber matrix), the anti–vibra ion ability can be modified. Accord ng to the effects of changing a lot of parameters, some comparative anal sis for the selections of materials were done where the EPDM rubber sample showed up not on y the high mechanical properties but also the effective p rformanceof the anti–vibration ability. In comparison with the requirements of the anti–vibration rubber pads, the hardness and the anti–vibration performance values of the sample with the recipe using with about 45% carbon black, 1% triethanolamine tea and 1% sulfur got the best properties at approximately 62 Shore A and 72%, respectively. Based on this research, there are numerous applications for anti–vibration systems using EPDM rubber containing carbon black in building construction, machine techniques, environment and health.